Recycling PET bottles is an important part of realizing a circular economy. By converting used PET bottles into recycled materials, new products can continue to be manufactured, thus reducing waste and extending the life cycle of the resource. One of the best ways to do this is to utilize recycling machinery to process them into recycled PET bottle flakes, which usually require a series of processes.
Benefits Of Recycling PET Bottles
First, plastic recyclers can sell processed recycled PET bottle flakes to manufacturers who need to use the material. Using recycled PET bottle flakes as a raw material for production usually reduces production costs. The lower cost of recycled PET compared to newly produced PET materials can help manufacturers reduce production expenses and improve competitiveness.
What Companies Can Recycle PET Bottles?
- Beverage manufacturing plants: companies specializing in the production of beverages in PET bottles;
- Breweries: companies that produce beer in PET bottles;
- Food processors: companies that use PET bottles for food products;
- Plastic recycling company: a company specializing in the processing and recycling of all kinds of plastic waste, PET bottle recycling line can effectively process PET bottles and convert them into recycled materials;
- Manufacturer: Manufacturing companies that require large quantities of PET bottle flakes as raw material.
These companies typically produce high-quality recycled PET bottle flakes for sale or use in the manufacture of new PET products.
Learn more: Beneficiaries Behind The PET Recycling Line
High-Quality PET Flakes
High-quality PET bottle flakes tend to command a higher market value. Our PET bottle recycling machine can produce bottle flakes that meet the following standards.
- Moisture content: <0.5-1%
- pH: <8.0
- PVC content: < 100ppm
- PE/PP content: < 200ppm
- Impurity content: ≤300-500mg/kg
- Powder content: ≤ 2000-3000mg/kg
- Particle size: < 16-18mm
Steps to Recycle PET Bottles
Step 1: Collection Of Raw Materials (PET Bottles)
Classification from the degree of soiling of raw materials: Collected PET bottles can be divided into two categories according to their degree of soiling: virgin materials and post-consumer plastics. The raw material for some manufacturers is usually clean virgin material, such as waste and expired bottles from production, which produces higher-quality bottle flakes. Post-consumer plastics, on the other hand, may contain more impurities and contaminants and require more complex cleaning processes.
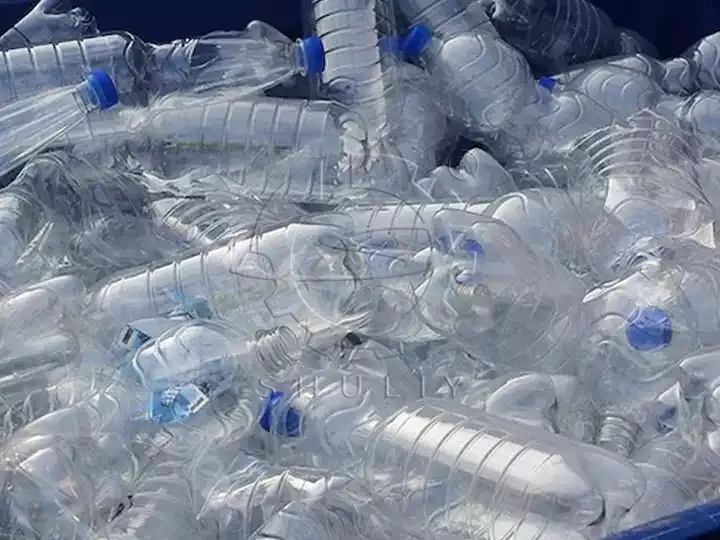
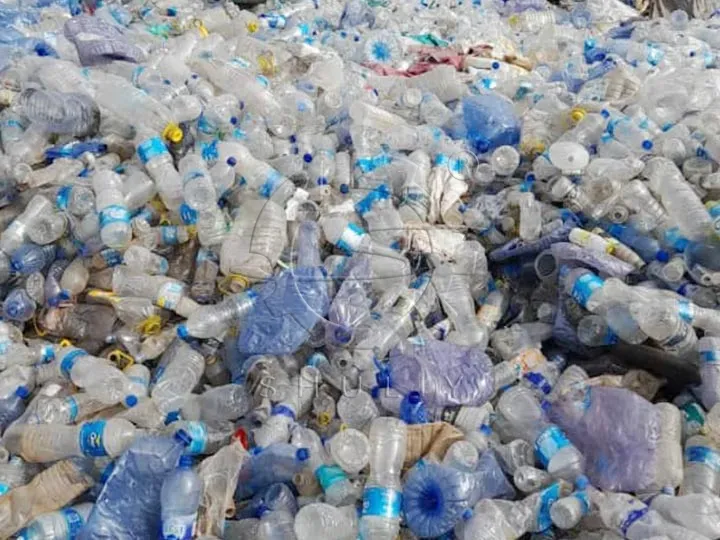
Classification from PET bottle color: PET bottle classification by color helps to improve the quality of recycled bottle flakes. The color grades from high to low are pure white flakes, blue and white flakes, green flakes, yellow flakes, and miscellaneous flakes, and different colors of bottle flakes have different demands and prices in the market.
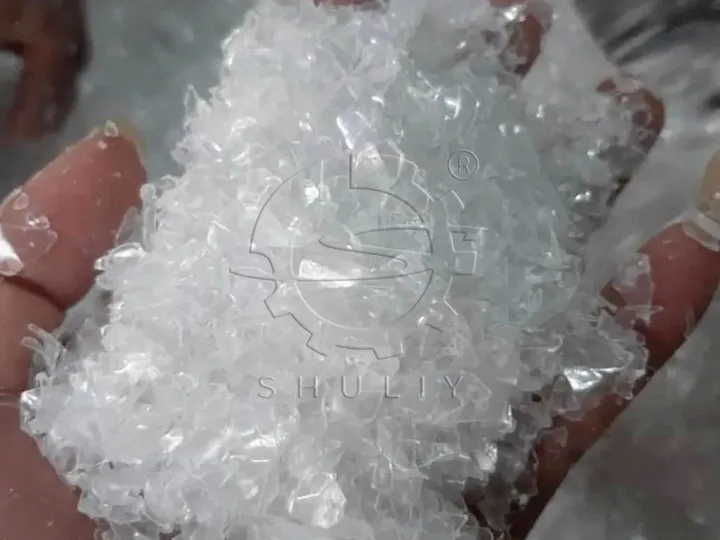
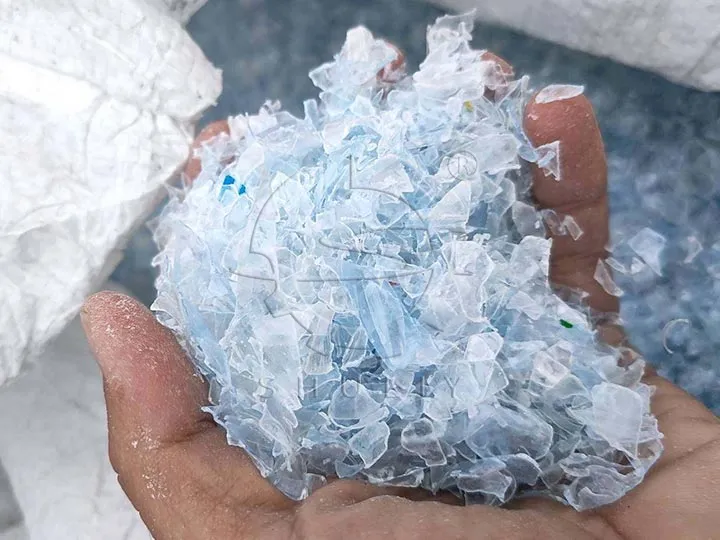
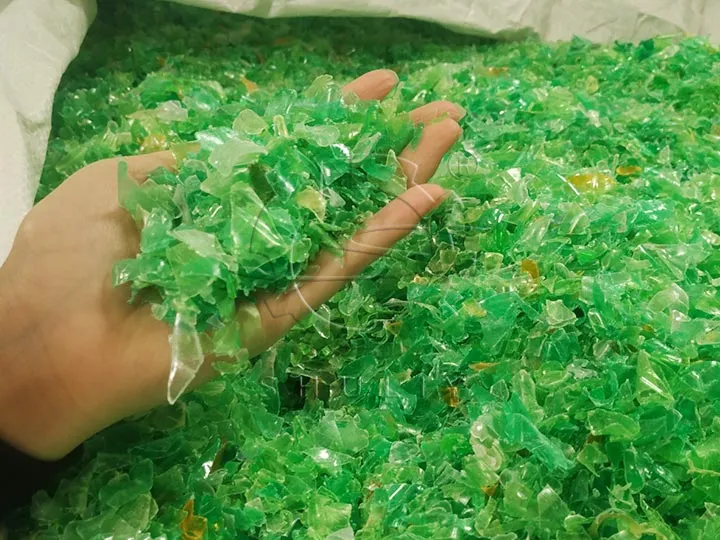
You can read: Factors Affecting The Fluctuation Of Recycled PET Bottle Flake Recycling Price
Step 2: Site Requirements
The site requirement for our PET bottle washing line is 500 to 1,000 square meters. If the production line is larger, a larger site is required to ensure that the equipment can be installed and moved smoothly.
The site should have enough space to accommodate all types of equipment and allow flexibility for future expansion and maintenance. In addition, the site should take into account the layout and orientation of the equipment to ensure ease of operation and safety.
Step 3: PET Bottle Recycling Machine Configuration
To recycle PET bottles, the following equipment is usually required:
PET Bottle Label Remover Machine
- Remove PVC labels from PET bottles;
- 98% label removal from round bottles;
- 93% label removal from flat bottles;
- Reduce PVC content to 100-300mg/kg;
- Blade material: carbide blade.
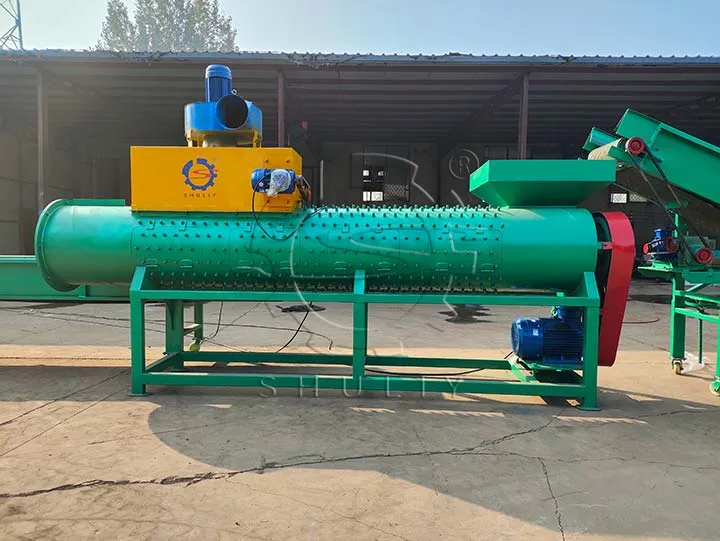
Plastic Bottle Shredding Machine
- Crushing PET bottles into flakes;
- Blade material: 9CrSi;
- Powerful motor drive;
- Sieve mesh aperture size: 16-18mm, can be customized;
- Water can be filled into the machine.
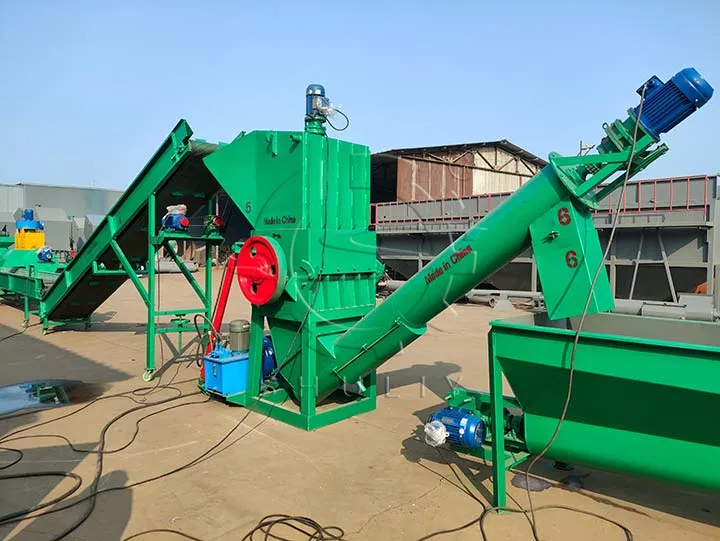
- Separation of PP bottle caps and PVC labels from PET bottle flakes;
- PET bottle flakes sink, caps and labels float;
- control polyolefin content at ≤200-300 mg/kg;
- For lighter PET bottle flakes, deep water tanks are provided.
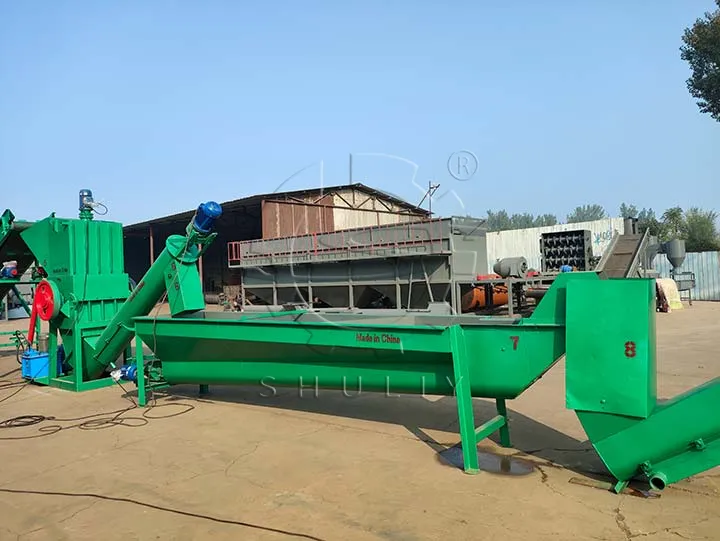
PET Flakes Hot Washing Machine
- PET bottle flakes are cleaned by heat and agitation;
- Cleaning powder or lye may be added;
- Water temperature should be maintained between 85-95 degrees;
- The cleaning time should be 30-45 minutes;
- Electromagnetic heating is used.

- Inside, there are rubbing plates and rubbing strips to scrub the bottle pieces;
- Cleaning off the lye brought out from the hot wash pot and lowering the pH value to less than 8;
- The machine is inclined at 45 degrees for easy drainage.
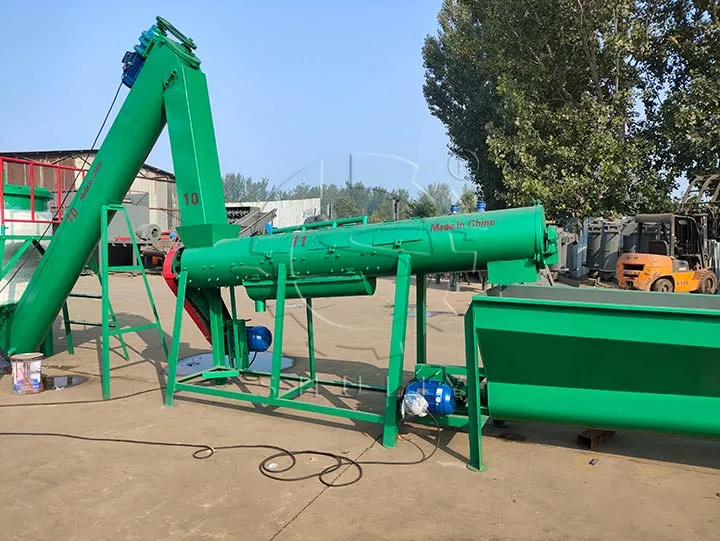
Horizontal Dryer and Wind Separator
- Horizontal dryer removes moisture from bottle flakes;
- The dryness can reach 95%-98%;
- Adding drying pipes, the moisture can be controlled at 0.5%-1%;
- The wind separator is used to remove the residual fine logo and dust;
- Impurity content/(mg/kg)≤300-500
- Powder content/(mg/kg)≤2000-3000
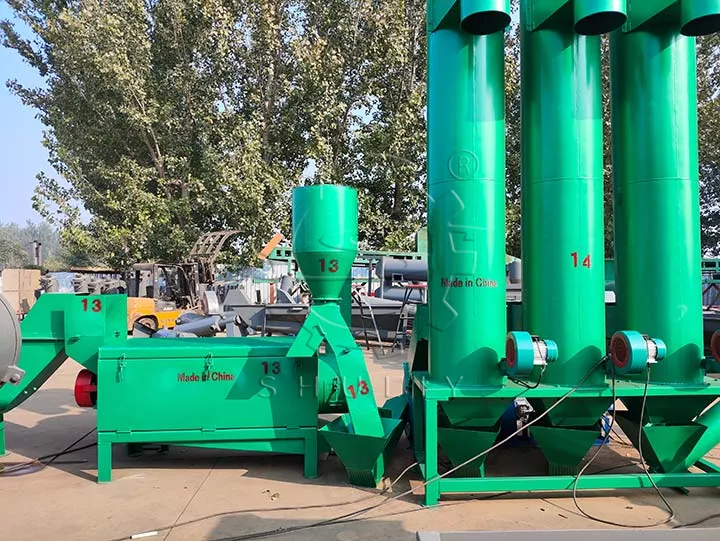
Step 4: How Is The Equipment Installed?
We will provide you with an installation guide, and our technical team can also provide remote video guidance or on-site assistance to ensure a smooth installation process.
When installing the equipment, you first need to determine the specific location of the equipment according to the layout of the plant to ensure that each machine has enough operating space and access.
Secondly, install the recycling machine step by step following the design sequence of the production line and ensure that supporting facilities such as power supply, water source, and drainage channels are in place.
Finally, the installation of the completed equipment for commissioning to ensure its normal operation in the actual production.
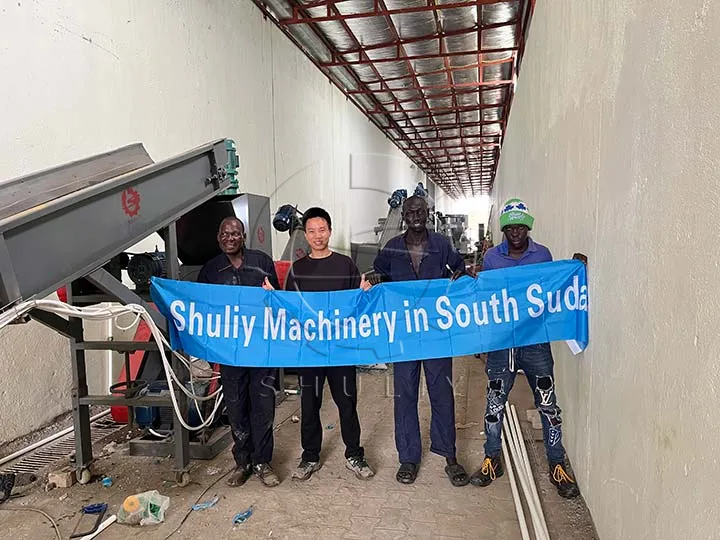
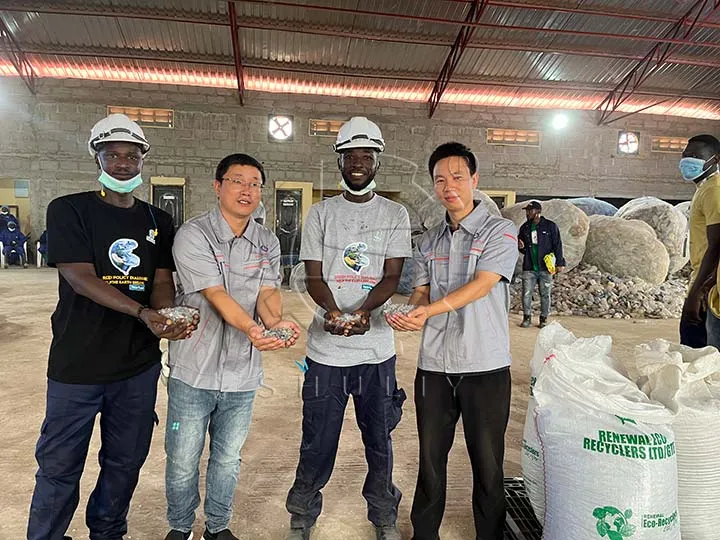
Step 5: Number of Laborers
For a 1000kg/h PET bottle recycling line, 6-8 laborers are usually required. The exact number of personnel can be adjusted according to the output, the degree of automation of the equipment, and the actual needs of the plant to ensure the efficient operation of the line.
FAQs of PET Bottle Recycling Machine
What Is The Production Range Of This Line?
The production capacity of our PET recycling line ranges from 500kg/h to 6000kg/h, which meets the needs of most customers.
Is The Required Configuration For Recycling PET Bottles Fixed?
Not fixed. Our equipment configurations are very flexible and can be selected according to actual needs.
What Is The Delivery Date?
20-25 days.
How Long Is The Warranty?
Our warranty is one year. During this period, any problem with the machine, you can contact us and we will solve it for you.
Contact Us To Get
If you plan to recycle PET bottles and need an efficient PET flakes washing line, you can contact us and we will provide it for you:
- Detailed Product Description
- Tailor-made solutions
- Factory Tour
- Quotation and contract signing
- Equipment Manufacturing and Delivery
- Online guidance or on-site installation assistance
- After-sales service and technical support