Plastic pellet machines play a crucial role in the processing of waste plastics and the preparation of recycled pellets. Let’s delve into the operation and performance of this machine, addressing questions you may have been curious about.
Different Materials On A Single Pelletizing Line?
The design of pelletizing machines is not universal. Different types of plastics have varying melting characteristics and extrusion requirements. Therefore, using the same plastic pelletizing line for different materials may result in mismatched parameters such as temperature and pressure, affecting the overall production effectiveness. Hence, it’s generally not recommended to process different types of plastics on the same line.
There are some other common problems when it comes to plastic pelletizing lines. Taking the plastic recycling granulating line that processes one tonne of plastic per hour as an example, the power consumption for processing one tonne of plastic is about 500 degrees, while the whole production line can be completed by only 3-4 workers. Our plastic recycling granulating line not only ensures high production efficiency and product quality but also makes the production process more energy efficient and labor costs more economical.
Temperature Settings For Pelletizing Machine
For the pelletizing of PP and PE, temperature control is paramount. Typically, the temperature needs to reach 240 degrees, and the plastic pellet machine’s operating temperature can go as high as 500 degrees. This ensures that the plastic fully melts at high temperatures, facilitating the subsequent extrusion process.
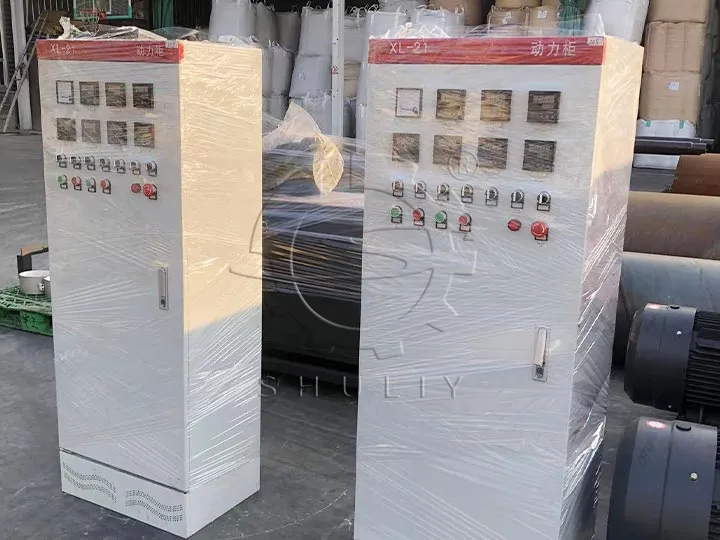
Diameter Of The Line Produced By The Die Head
The diameter of the extruded line in the pelletizing process is usually around 3.2mm. This size is achieved through the design and adjustment of the plastic pellet machine, directly influencing the specifications and uses of the resulting pellets.
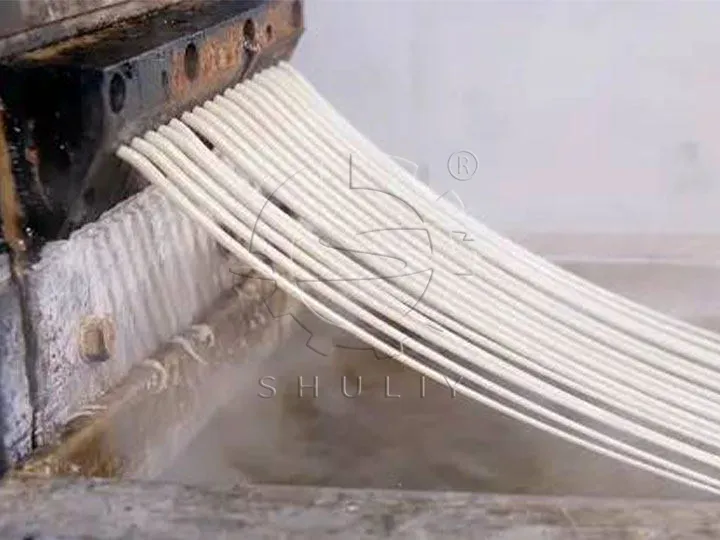
What Is The Working Principle Of Pelletizing Machine?
The working principle of the plastic pellet machine is based on the processes of high temperature and screw extrusion. Initially, the machine needs to be preheated to bring the entire system to the appropriate operating temperature. Then, plastic raw materials are fed into the machine. Through the force of the screw extrusion at high temperatures, the plastic melts and is extruded, ultimately forming pelletized plastic.
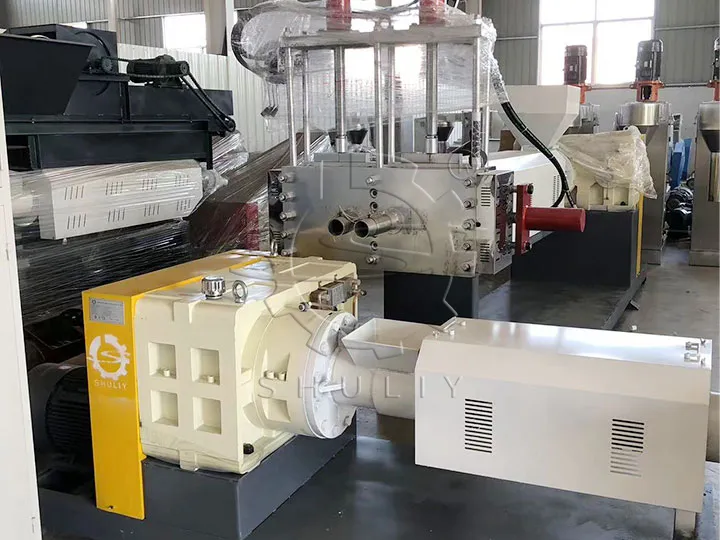
Problems With Die Head Changing Screens
Some customers have asked how often the die head of the recycling granulator machine needs to change the screen. Can the screen be reused?
The frequency of net changes in the mold head depends on the cleanliness of the material. If the material is relatively dirty, frequent changes are required. However, for cleaner materials, a week or so is sufficient. The die nets of the plastic pellet machine can be reused, by burning the screens and cleaning them.
How Are Plastic Pellet Machine Models Differentiated?
Pelletizing machine models are typically differentiated based on the inner diameter of the screw. The size of the screw’s inner diameter directly relates to the production capacity and applicable range of the pelletizing machine.
By understanding the operational principles and key parameters of plastic pellet machines, we gain insight into the pivotal role these devices play in the realm of waste plastic recycling. From material selection to temperature control, each aspect is crucial, influencing the quality and applications of the final recycled pellets. When using pelletizing machines, scientific and rational operation, coupled with regular maintenance, are critical factors in ensuring production efficiency and product quality.