The horizontal dryer is a machine for the efficient dewatering and drying of materials such as plastic sheets, films, and PET flakes. It separates moisture from the material by centrifugal force generated by high-speed rotation, ensuring that the moisture content is reduced to the desired level.
Our plastic dewatering machine is made of high-quality materials with sturdy and durable structure, high corrosion resistance, low maintenance cost, and long service life. The appearance of the equipment can be customized according to customers‘ needs, which can better meet customers’ production requirements.
Features of Plastic Chips Dryer Machine
- The machine is suitable for a wide range of applications, such as PET bottles, PP/PE/PVC/ABS flakes, and so on.
- Reasonable design, low noise, and easy to maintain, you can easily open the body to remove the screen impurities inside the dryer.
- Good dewatering effect, able to control the moisture in the plastic material below 3%-5%.
- It can be used with a drying tube to control moisture at 0.5%-1%.
- The screen, rotor, and body are made of high-quality stainless steel, which makes the horizontal dryer sturdy and durable.
- In addition to dewatering, it also removes fine debris such as plastic sand.
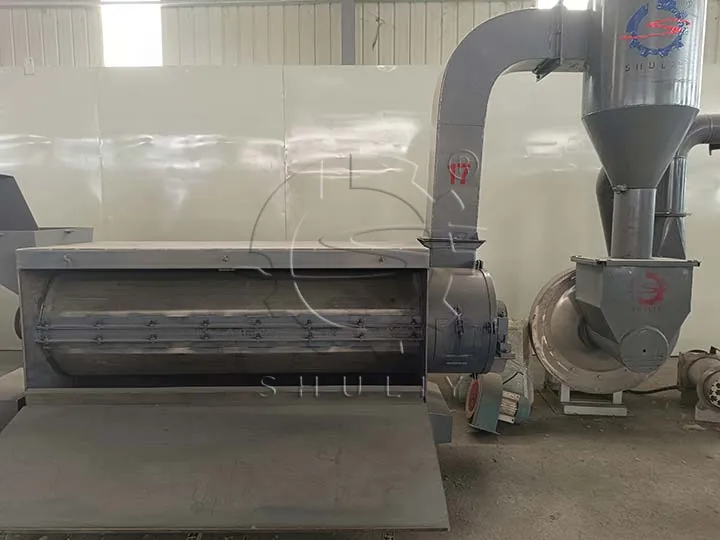
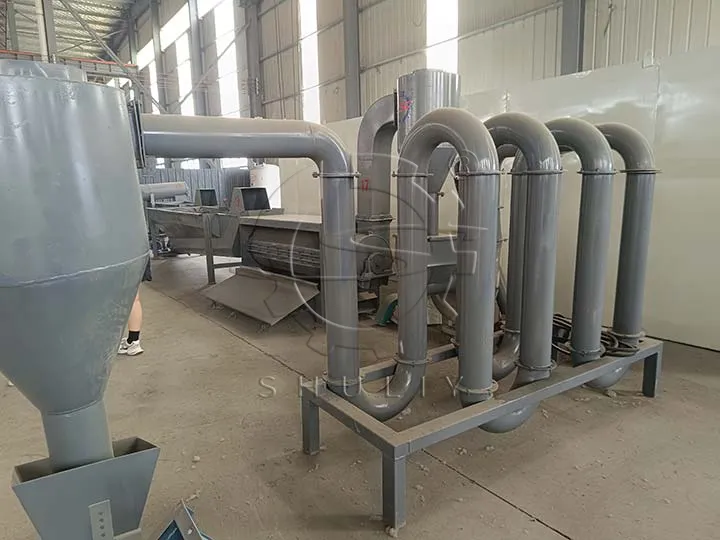
Application Of Horizontal Dryer
Plastic flake dewatering machines are widely used in a variety of plastic recycling lines, including film pelletizing lines, hard washing and pelletizing lines, and PET bottle flake washing lines. It is capable of efficiently dewatering and drying different types of plastic materials, whether it is soft plastic film, rigid plastic flakes, or PET bottle flakes, the centrifugal dryer plays a key role in the production process, ensuring that the dryness of the material meets the needs of subsequent processing, and improves the efficiency and product quality of the entire production line.
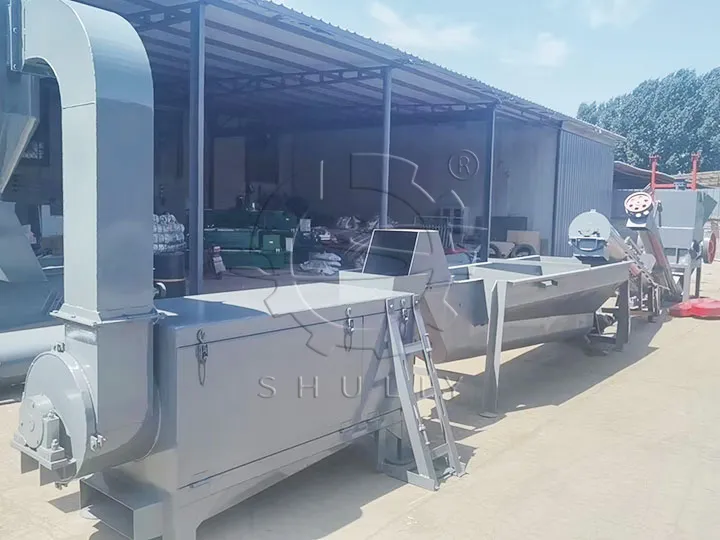
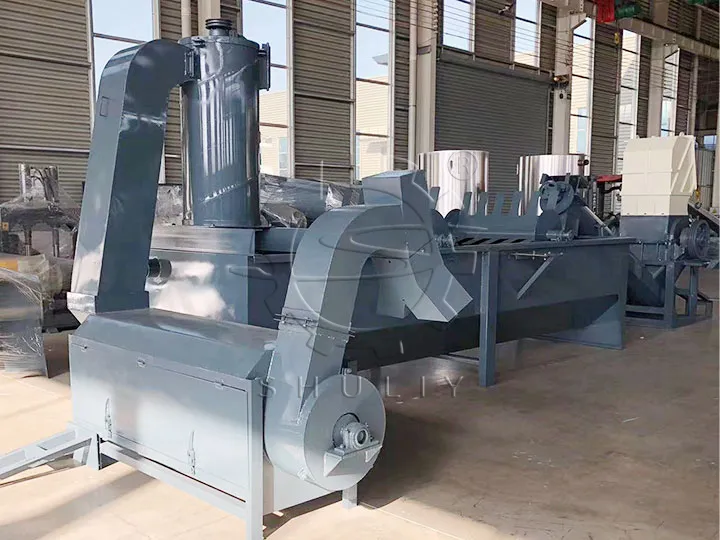
Working Principle of Horizontal Dewatering Machine
The working principle of the horizontal dryer is based on the centrifugal force generated by the high-speed rotation to separate water or moisture from the plastic material. In operation, the plastic enters the rotating drum of the plastic chips dryer machine after which the motor is activated, causing the drum to rotate at high speed. This high-speed rotation generates an extremely strong centrifugal force. Through perforations or openings in the surface of the drum, the extruded moisture is effectively separated along with the centrifugal force, resulting in a drier plastic material.
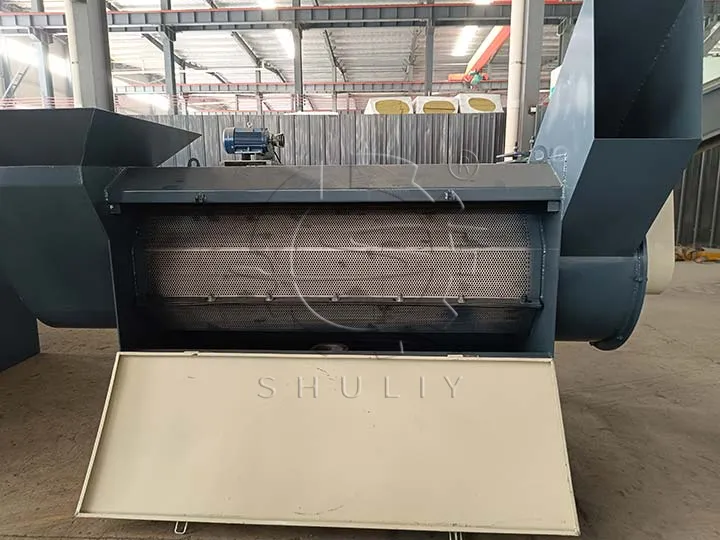
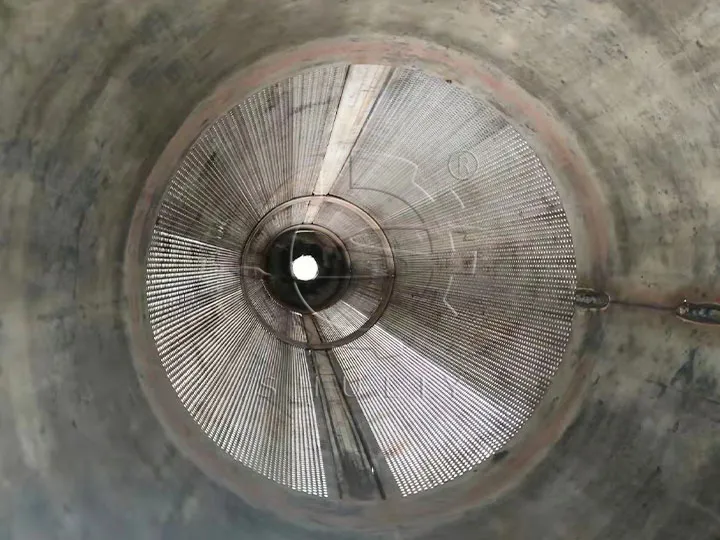
Working Video of Horizontal Dryer
Importance Of Plastic Dryer Machine
The use of dehydrators in recycled plastic pellet production lines and plastic recycling washing lines is critical for the following reasons:
- Reduction of smoke and pollution: In a film granulating line, if moisture is not effectively removed, the subsequent pelletizing process may generate a large amount of smoke and increase environmental pollution.
- Reduced energy consumption: The dewatering machine reduces production costs by initially removing water from the plastic material, reducing heating time and energy consumption during subsequent pelletizing.
- Improved pellet quality: the horizontal dryer ensures that the material reaches the proper level of dryness before entering the pelletizer, avoiding unsmooth pellet surfaces and internal porosity, thus guaranteeing consistency in the final product.
- Ensure the quality of recycled flakes: the moisture content of recycled sheets must be less than 3%-5%. The dewatering machine can effectively control the moisture and ensure uniform and stable quality of the sheet.
Specifications
The model of our plastic chips dryer machine is SL-550, the output is 1000kg/h and the filter pore size is 4mm. In addition, we have a variety of models and appearances to choose from, and we can also provide customized services.
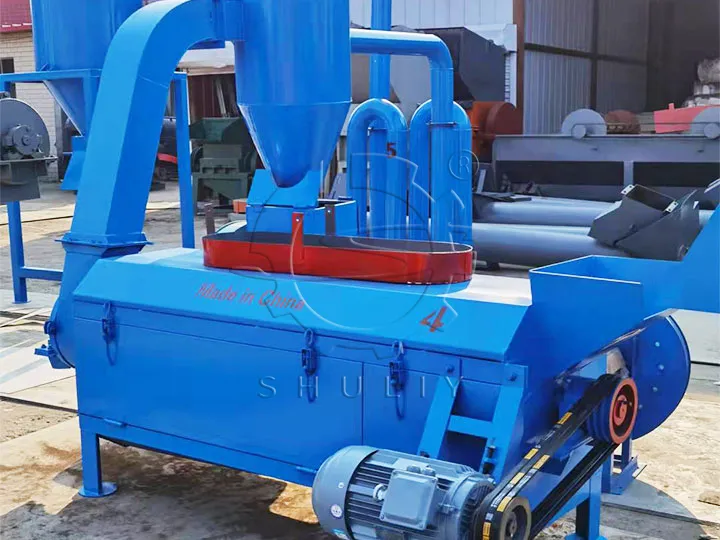
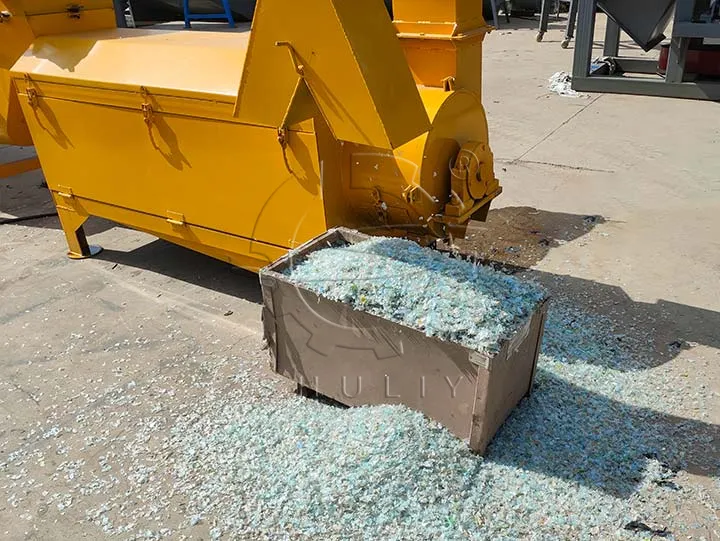
Plastic Flake Dewatering Machine Export Cases
We successfully customized a plastic flake dewatering machine for a customer in Indonesia. This customer is engaged in plastic recycling and needs to clean and dry 1cm-sized LDPE film pieces. To avoid leakage, we customized the size of the dryer screen. In addition, we equipped the drying pipe to meet the customer’s requirement of less than 0.5% final moisture content.
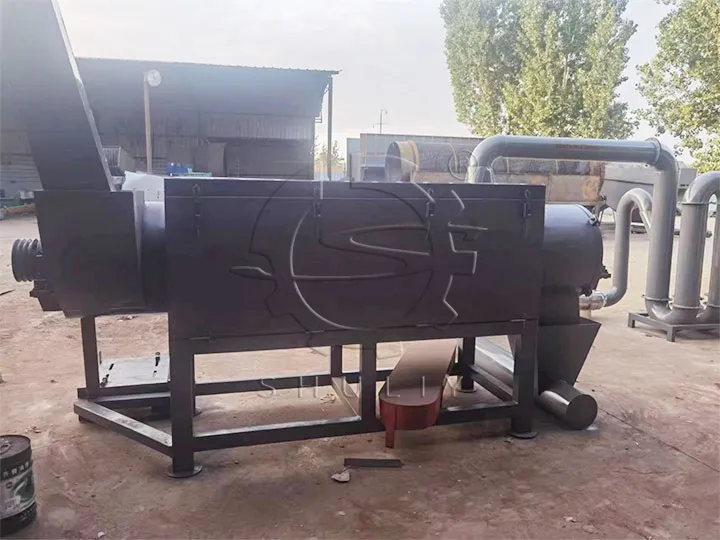
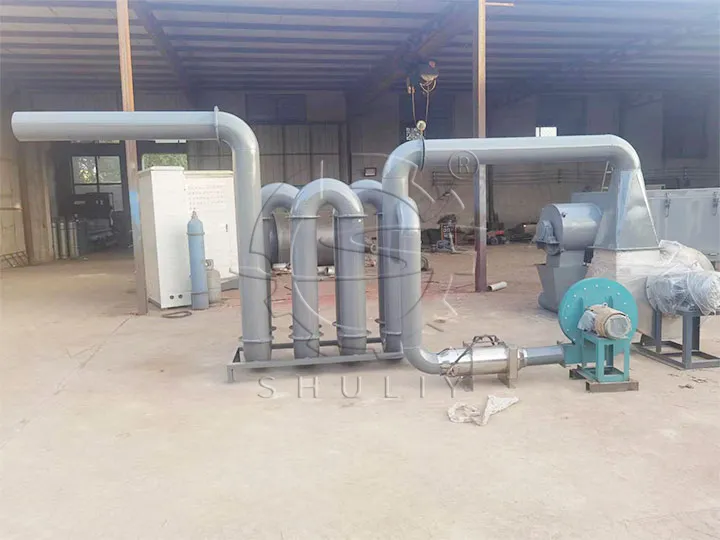