Mesin pemotong pelet digunakan untuk memotong plastik menjadi pelet plastik setelah dicairkan dan ditarik stripnya, dan bilahnya adalah kunci untuk memotong bahan baku plastik menjadi pelet yang seragam. Desain, bahan, dan karakteristik pengoperasiannya berperan penting dalam menentukan kualitas pelet yang dihasilkan.
Desain dan Pilihan Material Pisau
Konstruksi pisau memainkan peran penting dalam memastikan pemotongan yang efisien dan konsisten. Produsen mesin daur ulang plastik dengan cermat mengonsep profil pisau, termasuk bentuk, ukuran, dan sudut pemotongan, untuk mengoptimalkan proses pemotongan. Pilihan material pisau juga sama pentingnya. Mesin pemotong pelet kami biasanya terbuat dari material berkualitas tinggi dan tahan lama seperti karbida untuk menahan tekanan mekanis serta keausan yang ditemui selama proses pemotongan.
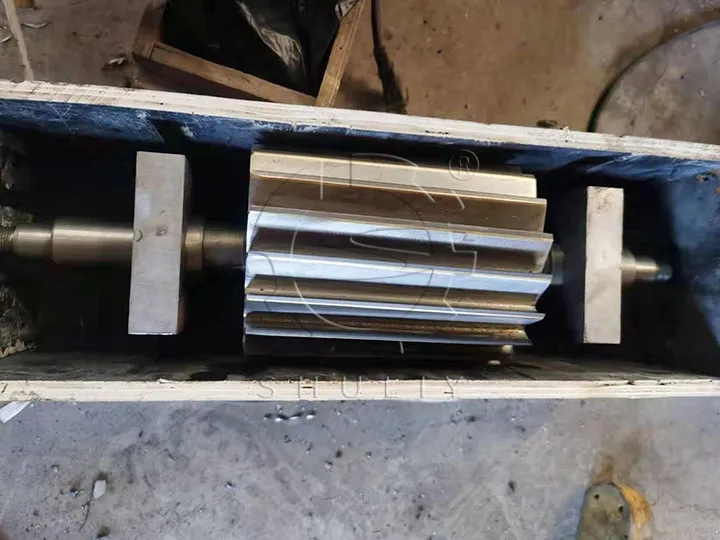
Kecepatan Rotasi Mesin Pemotong Pelet
Kecepatan putaran yang tinggi merupakan ciri khas dari sudu-sudu ini. Kecepatan putaran dipilih secara cermat sesuai dengan jenis plastik yang akan diproses, ukuran partikel yang diperlukan, dan konfigurasi ruang pemotongan. Hal ini memungkinkan bilah memotong bahan plastik dengan cepat dan bersih, sehingga menghasilkan pelet yang presisi dan seragam.
Gesekan dan Pelumasan
Selama proses pemotongan berputar berkecepatan tinggi, gesekan antara bilah dan pelet plastik menghasilkan panas dan keausan, yang mempengaruhi efisiensi dan presisi pemotongan. Pelumasan teratur dapat secara efektif mengurangi gesekan, mengurangi panas yang dihasilkan selama proses pemotongan, memperpanjang masa pakai bilah, dan pada saat yang sama memastikan kualitas pemotongan butiran.
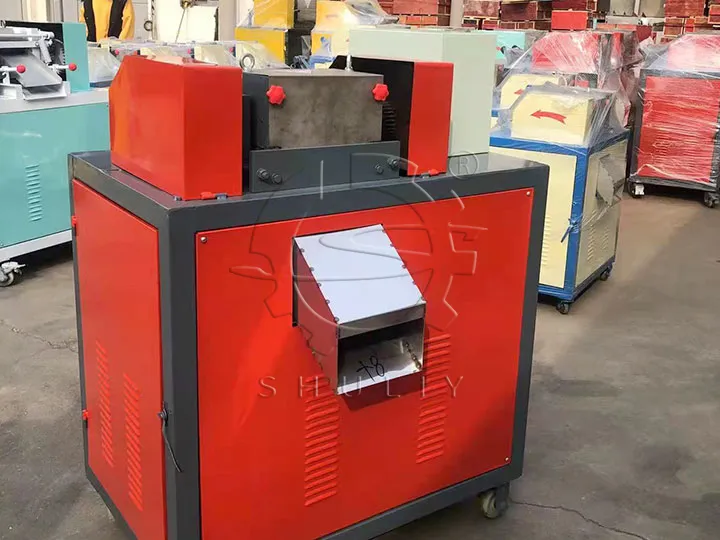
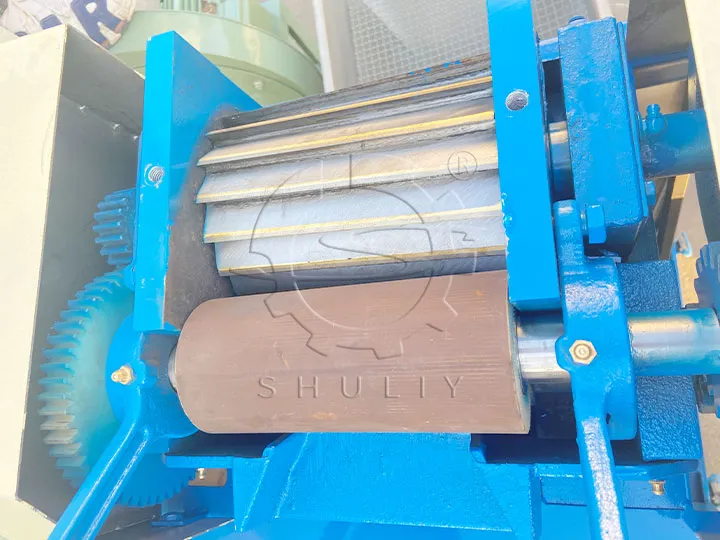
Perawatan dan Penggantian Pisau
Mengingat sifat pisau yang berkecepatan tinggi dan sifat abrasif bahan plastik, perawatan pisau sangatlah penting. Pemeriksaan rutin, penajaman, dan penggantian bilah yang aus memastikan pemotong pelet terus beroperasi pada efisiensi puncak.