Pembuat pelet plastik dalam pengolahan bahan baku plastik, terkadang akan terjadi kasus pecahnya strip saat granulasi, sehingga menimbulkan gangguan pada proses produksi. Ada banyak penyebab fenomena ini, yang akan kita bahas secara detail di bawah ini.
Alur Kerja Ekstruder Daur Ulang Plastik
Pertama, kita perlu memahami alur kerja pembuat pelet plastik untuk memahami penyebab kerusakannya. Pertama, bahan baku masuk ke granulator plastik, yang kemudian dipanaskan dan dicairkan. Kemudian, mereka diekstrusi ke dalam kepala cetakan melalui sekrup, dan strip plastik kontinu diekstrusi melalui kepala cetakan. Begini cara kerja mesin, selanjutnya kita bahas penyebab dan solusi batang patah.
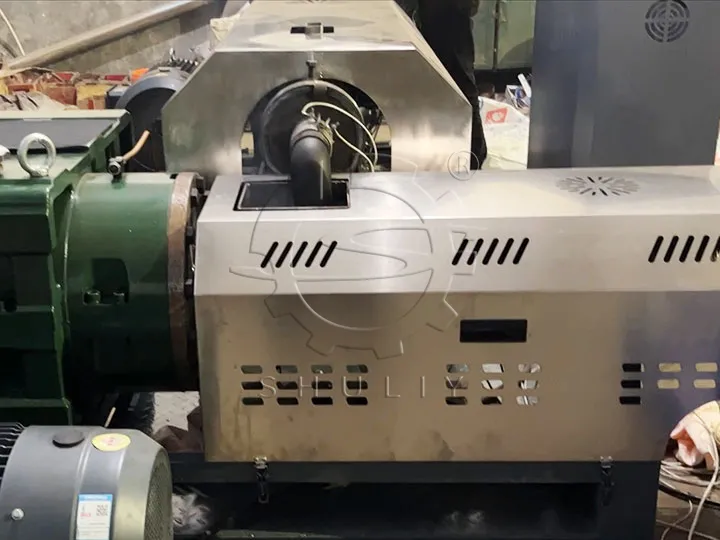
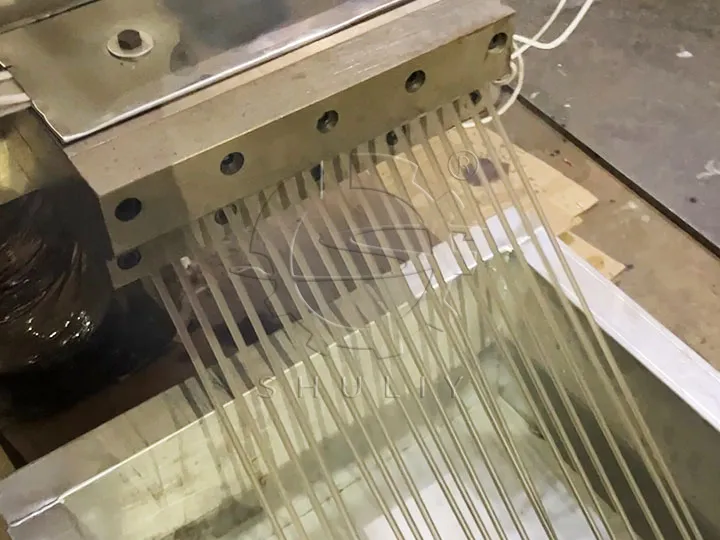
Penyebab Patah Batang Pada Pembuat Pelet Plastik
- Kualitas bahan baku yang buruk: Kualitas bahan baku plastik secara langsung mempengaruhi efek granulasi. Jika bahan mentah mengandung kotoran, kelembaban tinggi atau partikel tidak rata, dan masalah lainnya, ekstruder daur ulang plastik dapat dengan mudah menyebabkan fenomena batang pecah dalam proses kerja.
- Kegagalan Mesin: Bagian ekstruder daur ulang plastik yang rusak atau tidak disetel dengan benar juga dapat menyebabkan patahnya batangan. Misalnya, masalah seperti cetakan yang aus, sekrup yang aus, dan pengaturan suhu yang tidak tepat dapat mempengaruhi kontinuitas granulasi.
- Pengoperasian yang tidak benar: Tingkat teknis dan pengalaman pengoperasian operator sangat penting untuk efek kerja peralatan granulasi plastik. Metode pengoperasian yang salah dapat menyebabkan kerja mesin tidak stabil, yang dapat mengakibatkan patahnya batangan.

Bagaimana Menyelesaikan Masalah Batang Patah Selama Granulasi?
- Pemilihan bahan baku berkualitas tinggi: Pastikan penggunaan bahan baku plastik berkualitas baik, tidak ada kotoran, kelembapan sedang, dan secara efektif dapat mengurangi terjadinya patah batangan.
- Perawatan dan Inspeksi Reguler: Rawat pembuat pelet plastik secara teratur, periksa apakah cetakan, sistem pemanas, sistem kontrol suhu, dan suku cadang lainnya normal, dan ganti suku cadang yang rusak tepat waktu untuk memastikan pengoperasian normal mesin.
- Penyesuaian parameter yang wajar: Berdasarkan karakteristik bahan baku dan kebutuhan produksi yang berbeda, atur parameter kerja dari pembuat pelet plastik secara wajar, termasuk suhu, tekanan, kecepatan, dll., untuk memastikan proses granulasi yang kontinu dan stabil.
- Pelatihan operator: Memberikan pelatihan profesional bagi operator untuk meningkatkan keterampilan pengoperasian dan pengalaman kerja, menstandardisasi proses pengoperasian, dan menghindari masalah patah tulangan akibat pengoperasian yang tidak tepat.
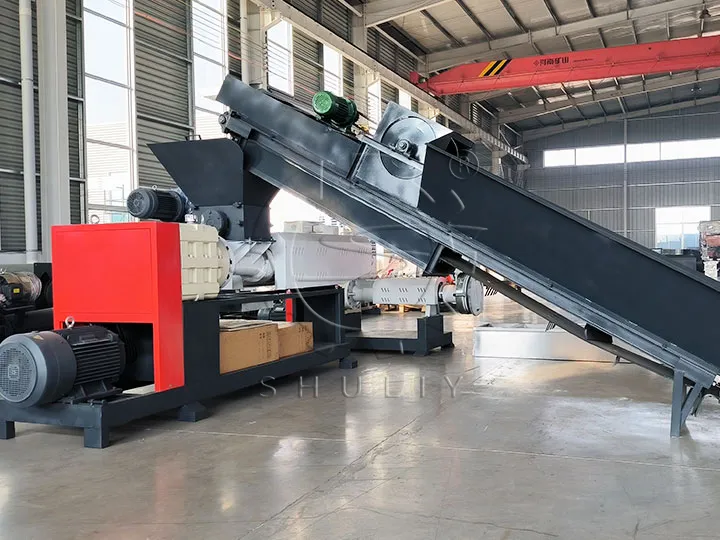
Singkatnya, fenomena strip pecah saat membuat granulasi pembuat pelet plastik mungkin disebabkan oleh berbagai alasan, namun pemilihan bahan baku yang wajar, perawatan mesin yang teratur, metode operasi ilmiah, dan tindakan lainnya, dapat secara efektif mengatasi masalah ini, meningkatkan efisiensi produksi peralatan granulasi plastik dan kualitas produk, serta memberikan kontribusi yang lebih besar terhadap daur ulang plastik.